We produce non-woven fabrics for interior and exterior using modern machinery and technology - needle punching lines, airlay, chemical lines, surface treatment lines for velouring and spraying, powdering, punching and forming machines.

Needle punching
PRINCIPLE
From the input material (fibre staple) a layer of fibres, a web, is mechanically formed using a carding machine. The laying of several layers of web by a weblayer creates the fleece. The fleece is then fed between two perforated plates, through the holes of which the needles pass. The barbs of the needles catch the bundles of fibres, turn them perpendicular to the direction of passage of the material and pull them through the fleece. As the needles move backwards, the fibre bundles are ejected from the needles and hooked onto adjacent fibres. The fibrous fleece is stiffened, thinned or further bonded to the supporting substrate (fabric, film, etc.) by needling.
TECHNICAL PARAMETERS
Processed material = PP and PES staple, recycled fibres
Working width = 4 - 6,5 m
PRODUCTS
Automotive
Geotextiles
Technical textiles
Airlay
PRINCIPLE
Airlay technology creates a fabric structure from randomly oriented fibres interconnected by a binder. The input materials are mixed in an aerodynamic chamber. The resulting layer is then deposited on a perforated belt and carried into a thermal chamber where the heat and pressure of the upper belt melt the binder and compress the layer to the desired thickness. At the end of the line, the resulting fabric is formatted into plates or rolls.
TECHNICAL PARAMETERS
Processed material = polyester fibres - PES, polypropylene fibres - PP, mixtures of synthetic and natural fibres, recycled fibres - natural and synthetic fibres and recycled textiles
Area weights = 600 - 6000 g/m2
Product thickness = 5 - 200 mm
PRODUCTS
Green roofs
Automotive
Insulation
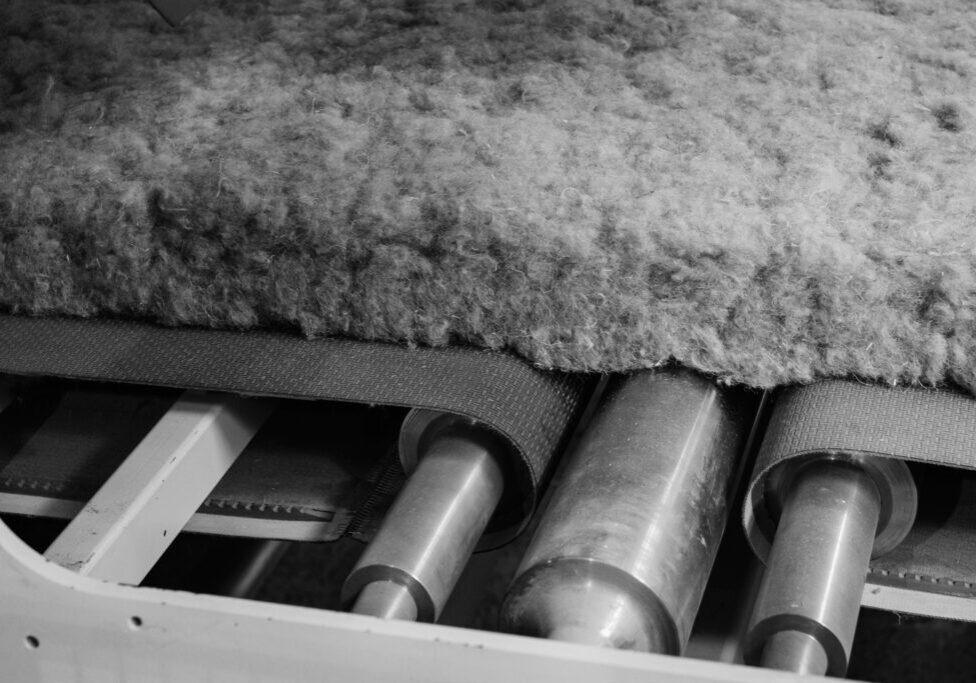
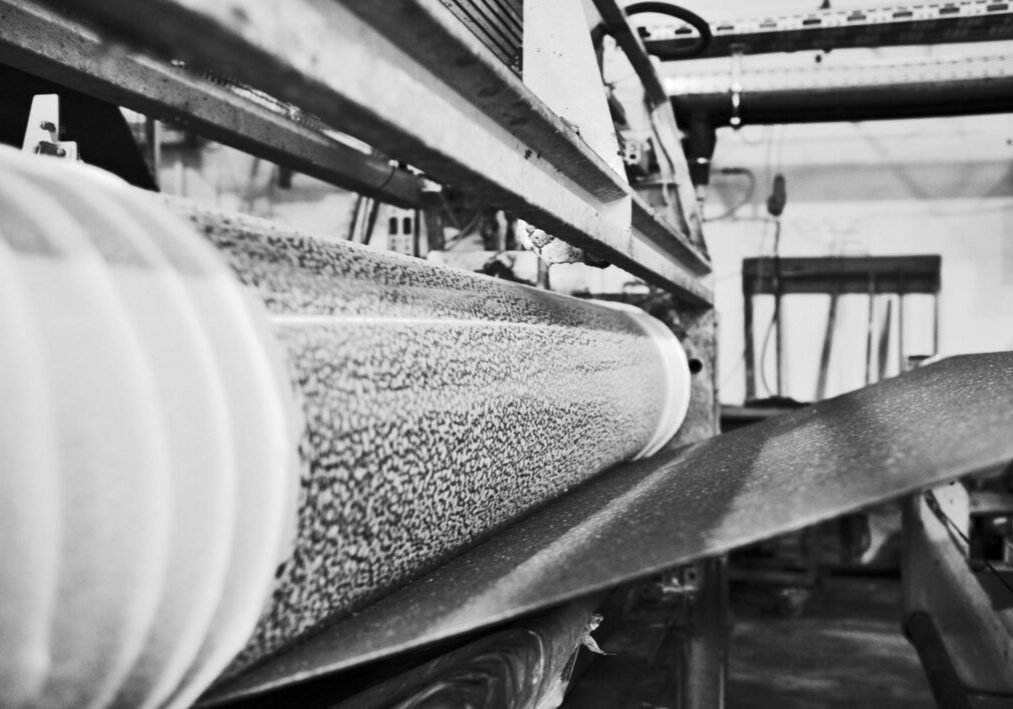
Foam impregnation
PRINCIPLE
Chemical treatment of nonwovens to strengthen the fibre layer or to achieve a desired property of the fabric. The treatment itself is carried out by impregnation - the application of a foamed binder and treatment to the structure of the fabric. The foam may be applied to one or both fabrics. In the case of applying the foam on both sides, a different binder or treatment can be applied to each side. The impregnation process is completed in a heat chamber in which the applied binder and treatment are activated. After cooling, the fabric is formatted to the desired width and shape, into a piece or roll.
PROCESSED MATERIALS
Non-woven needle-punched fabrics
Latex binders
TREATMENT FUNCTIONS
Flame resistant
Flame retardance
Velcro resistance
Fibre layer reinforcement
PRODUCTS
Automotive
Technical textiles
Powdering
PRINCIPLE
Chemical treatment of nonwovens to strengthen the fibre layer, to apply an adhesive layer or to join two materials by applying a thermoplastic powder binder. The activation of the binder takes place in a hot air chamber. After subsequent cooling, the fabric is formatted to the desired width and shape, cut into formats or rolled into rolls.
PROCESSED MATERIALS
Non-woven fabric
LDPE or HDPE binder powder
PE film
PRODUCTS
Automotive
Technical textiles
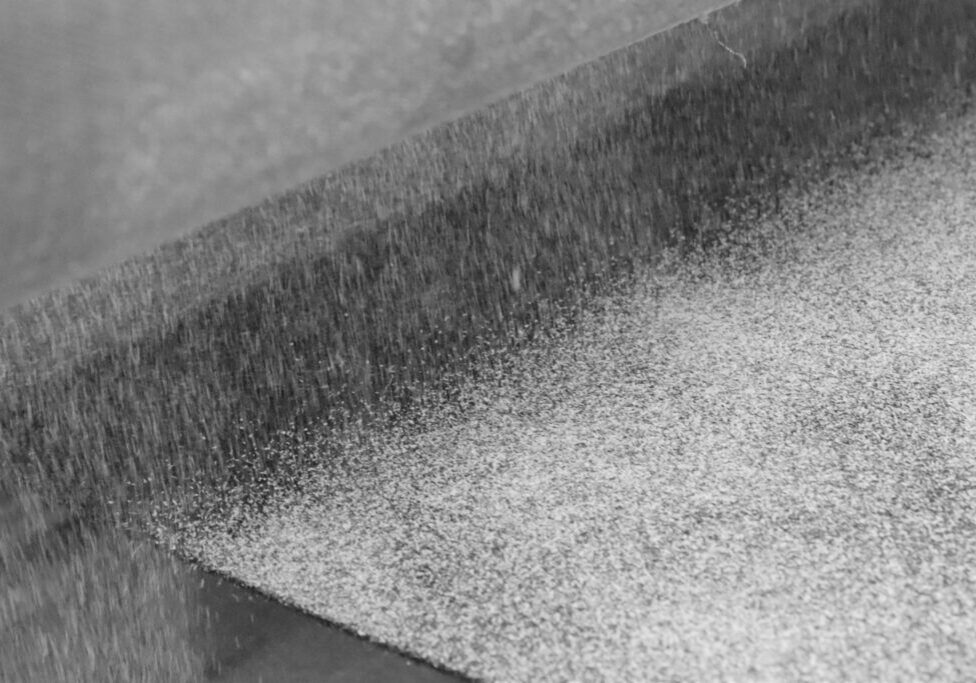
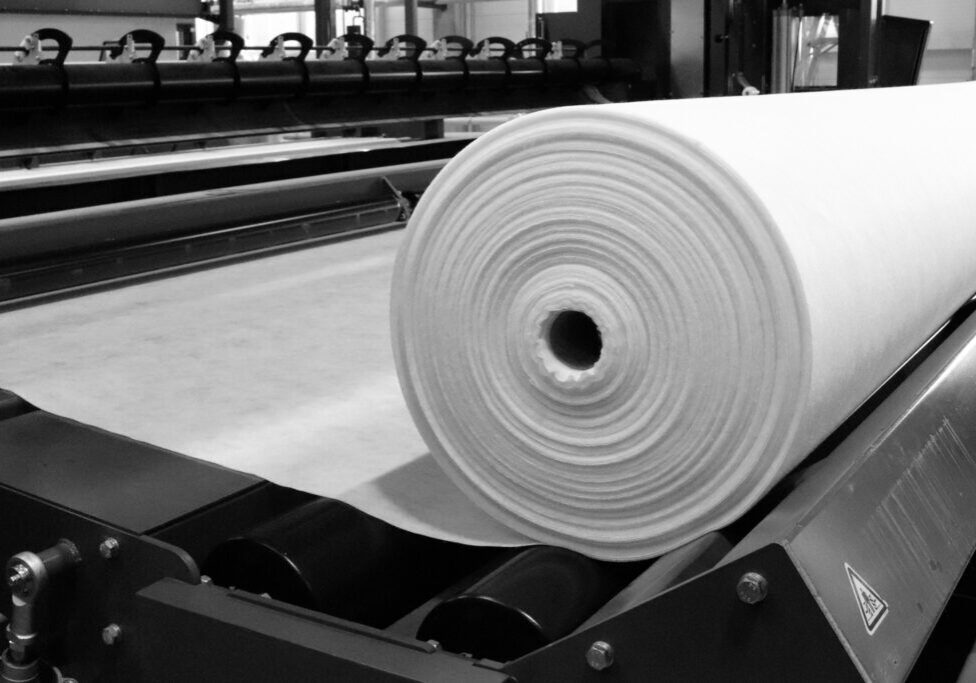
Calendering
PRINCIPLE
Reinforcement of the nonwoven fabric by heat and pressure, where the reinforcement itself occurs in the gap between two rollers, by heating and compressing the nonwoven fabric. The heating softens the fibres and the pressure causes the formation of bonding points between the fibres. Subsequent cooling strengthens the bond.
MATERIALS PROCESSED
Non-woven needle-punched fabrics
PRODUCTS
Geotextiles
Technical textiles
Velouring and trimming
PRINCIPLE
Mechanical treatment of non-woven needle-punched textiles in which a uniform surface is achieved and the textiles are given the appearance of velour or suede. The characteristic features of such products are their soft feel and velvety surface.
MATERIALS PROCESSED
Non-woven needle-punched textiles
PRODUCTS
Automotive

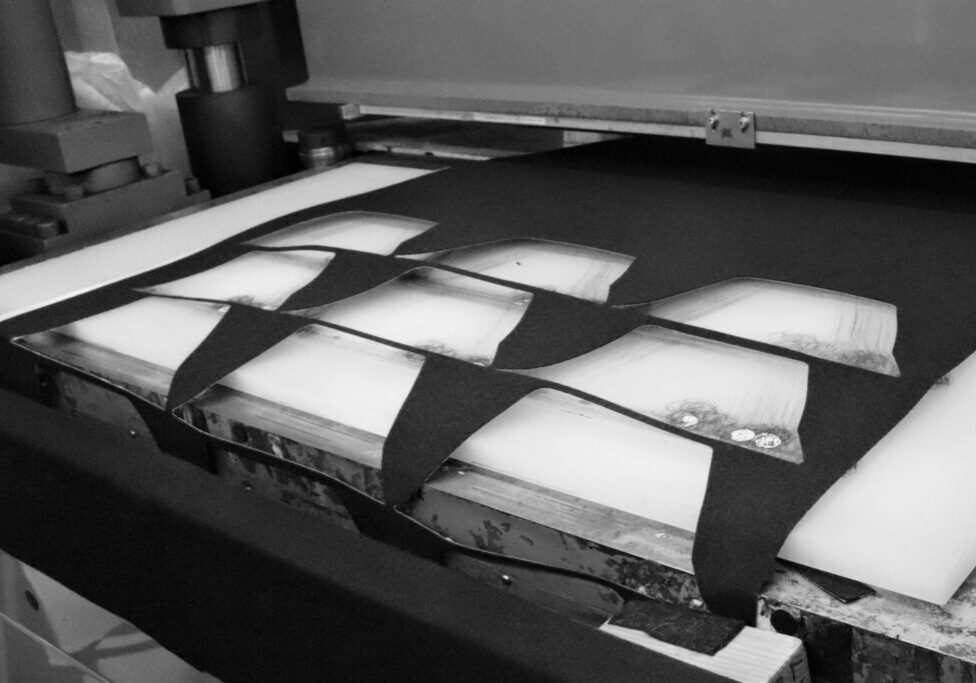
Punching and cutting
PRINCIPLE
Adjustment of the dimensions of the non-woven fabric on a cutting machine or production of the required shape on a pneumatic press or plotter.
MATERIALS PROCESSED
Needle-punched nonwovens
Airlay fabrics
PRODUCTS
Automotive
Insulation
Technical textiles
CERTIFICATION
We regularly test our products, both inhouse and at independent laboratories. The quality of our materials is also ensured by an advanced inspection system. The quality management system at RETEX is certified according to
ISO 9001, ISO 14001, IATF 16949, ISO 45001, ISO 50001, OEKO – TEX Standard 100 and IRIS Certification® Conformity assessment:2020 and based on ISO/TS 22163:2017
Our textiles also successfully undergo numerous customer audits.